Introduction:
The key to pharmaceutical success lies not only in the development of groundbreaking drugs but also in the meticulous adherence to Good Manufacturing Practices (GMP).
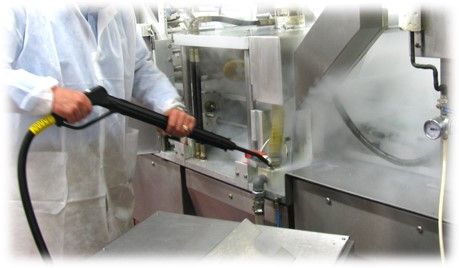
Equipment Integrity:
The GMP guidelines emphasize the paramount importance of preventing any substances associated with equipment operation from compromising the quality of pharmaceutical products. This includes lubricants, heating fluids, or coolants, which should not come into contact with intermediates or Active Pharmaceutical Ingredients (APIs). Deviations from this practice require thorough evaluation to ensure the material's fitness for use. The use of food-grade lubricants and oils is recommended wherever possible.
Continuous or campaign production of successive batches necessitates periodic equipment cleaning to prevent the accumulation and carry-over of contaminants. This underlines the need for a robust cleaning process.
Cleaning Process Design:
The cleaning process requires design and development prior to implementation in a manufacturing plant to ensure the cleaning process and equipment are acceptable for use.
There are four principal cleaning input parameters that can be varied for each step in the cleaning process. These four parameters are typically referred to as TACT (Time, Action, Concentration, and Temperature).
The four variables are interrelated and have a direct relationship on the success of each phase in the cleaning cycle.
PDA Technical Report No. 29 "Points to Consider for Cleaning Validation" - 3For example, cleaning agents may be heated to increase their effectiveness, plus Scientific rationale guides the selection of cleaning agents, considering their suitability to remove product residues, compatibility with equipment, ease of removal, and low toxicity.
The effect of each of these variables on soil removal should be determined and acceptable ranges established as part of the cleaning development effort. PDA Technical Report No. 29 "Points to Consider for Cleaning Validation" - 3.2.1
cleaning validation
Traditionally, cleaning validation involve three consecutive runs, each assessing worst-case process conditions. These conditions may include maximum dirty hold time, elapsed time in a campaign, or the lowest allowed temperature for manual cleaning processes. PDA Technical Report No. 29 "Points to Consider for Cleaning Validation" - 4.2.1
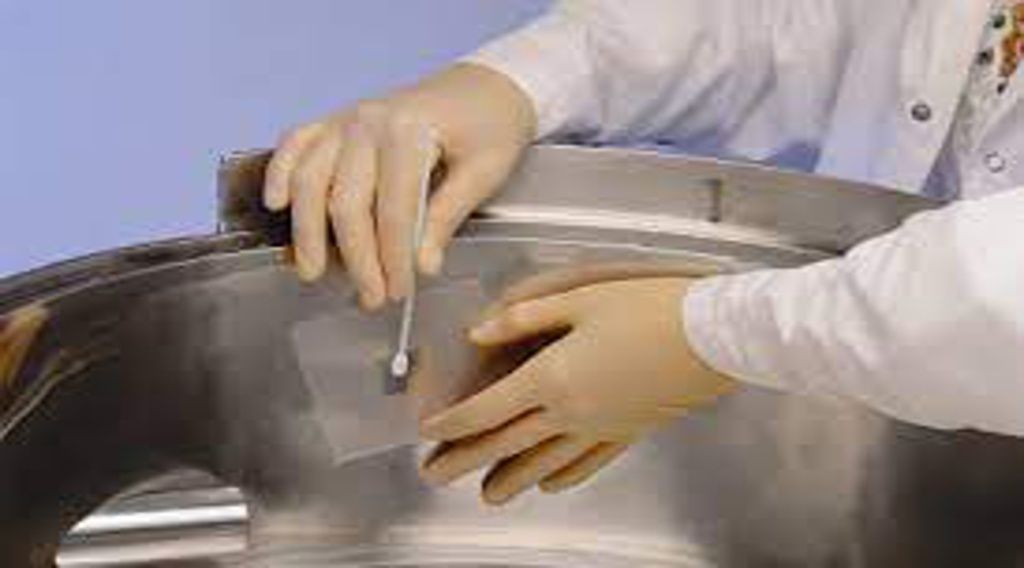
Grouping Products:
Products may be grouped together if they are manufactured on the same or equivalent equipment, and cleaned by the same cleaning procedure Products may be assessed for their relative cleanability by several methods. Relative cleanability may be affected by the nature of the active ingredients, of the excipients, and/or of degradation products.
Successful cleaning validation of the representative (worst-case) product means the cleaning of the other products in the group is also validated. PDA Technical Report No. 29 "Points to Consider for Cleaning Validation" - 4.3.1
Dedicated equipment
For equipment trains dedicated to manufacture of only one product, the concern about carryover of the active ingredient from one batch to the next is minimized.
As stated in the U.S. FDA guidance document, visually clean may be appropriate to address such a concern. However, cleaning validation may still be required because of concerns about other residues, such as degradants, cleaning agent and bioburden, carrying over to the next batch of the same product. PDA Technical Report No. 29 "Points to Consider for Cleaning Validation" - 5.9.13
Residue Limits:
Residue limits should be practical, achievable, verifiable, and based on the most deleterious residue. Limits can be established based on the minimum known pharmacological, toxicological, or physiological activity of the API or its most deleterious component. EU GMP ICH Q7A - 12.74
Sampling
Methods and Analytical Techniques:
- Direct surface sampling
- Rinse sampling
- Swabbing
- Placebo sampling.
PDA Technical Report No. 29 "Points to Consider for Cleaning Validation" - 6.1
Specific analytical methods
Validated analytical methods having sensitivity to detect residues or contaminants should be used. The detection limit for each analytical method should be sufficiently sensitive to detect the established acceptable level of the residue or contaminant. The method's attainable recovery level should be established. EU GMP ICHQ7A - 12.74Routine monitoring
Cleaning procedures should be monitored at appropriate intervals after validation to ensure that these procedures are effective when used during routine production. Equipment cleanliness can be monitored by analytical testing and visual examination, where feasible. EU GMP ICHQ7A - 12.76
Conclusion:
By delving into the intricacies of GMP standards, we reinforce our commitment to pharmaceutical excellence. Rigorous adherence to these guidelines ensures not only the quality of our products but also the trust of the patients relying on them.
References
1. ICH Topic Q 7 Good Manufacturing Practice for Active Pharmaceutical Ingredients
2. PDA Task Force on Technical Report No. 29, Points to Consider for Cleaning Validation
3. EudraLex, Volume 4, Part 1 Chapter 3: Premises and Equipment
4. WHO Technical Report Series, No WHO TRS 1033 Annex 2, Points to consider when including Health-Based Exposure Limits (HBELs) in cleaning validation
5. WHO Technical Report Series, No WHO TRS 1019 Annex 3, Goodmanufacturingpractices:guidelinesonvalidation, Appendix 3 Cleaning validation