Introduction:
At the heart of pharmaceutical manufacturing lies the crucial process of validation.
a comprehensive journey from defining a process to ensuring it consistently produces high-quality medicinal products.
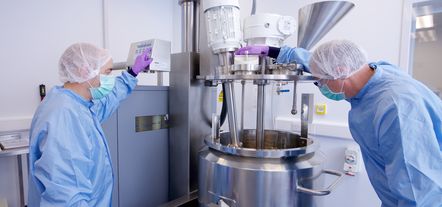
Understanding the Basics: Definitions and Regulatory Requirements
Process Validation is the documented evidence that the process, operated within established parameters, can perform effectively and reproducibly to produce a medicinal product meeting its predetermined specifications and quality attributes. EU GMP Eudralex Annex 15-12
Before any batch from the process is commercially distributed for use by consumers, a manufacturer should have gained a high degree of assurance in the performance of the manufacturing process such that it will consistently produce APIs and drug products meeting those attributes relating to identity, strength, quality, purity, and potency. FDA Guidance for Industry Process Validation: General - Principles and Practices -B
Navigating the Roadmap: Stages of Process Validation
process validation activities in three stages.
• Stage 1 – Process Design: The commercial manufacturing process is defined during this stage based on knowledge gained through development and scale-up activities.
• Stage 2 – Process Qualification: During this stage, the process design is evaluated to determine if the process is capable of reproducible commercial manufacturing.
• Stage 3 – Continued Process Verification: Ongoing assurance is gained during routine production that the process remains in a state of control.
FDA Guidance for Industry Process Validation: General - Principles and Practices -B
Critical Elements: Parameters and Attributes
Process validation should establish whether all quality attributes and process parameters, which are considered important for ensuring the validated state and acceptable product quality, can be consistently met by the process. EU GMP Eudralex Annex 15- 5.7
Validation Approaches:
There are three approaches to validation. Prospective validation is the preferred approach, but there are exceptions where the other approaches can be used. These approaches and their applicability are listed below.
· Prospective validation
· Concurrent validation
· retrospective validation
EU GMP ICH Q7- 12.41- 12.42- 12.43- 12.44
Quality Risk Management and Number of Validation Runs:
The number of process runs for validation should depend on the complexity of the process or the magnitude of the process change being considered.
For prospective and concurrent validation, three consecutive successful production batches should be used as a guide, but there may be situations where additional process runs are warranted to prove consistency of the process (e.g., complex API processes or API processes with prolonged completion times).
For retrospective validation, generally data from ten to thirty consecutive batches should be examined to assess process consistency, but fewer batches can be examined if justified. EU GMP ICH Q7 - 12.5
An initial validation exercise with three batches may need to be supplemented with further data obtained from subsequent batches as part of an on-going process verification exercise. EU GMP Eudralex Annex 15- 5.2
During on-going process verification exercise which may last for 25 batches to have statistically valid analysis of data there will be no relaxation of sampling plan, (i.e., the same validation batches intensive sampling plan)
Documentation: Validation Protocols
A process validation protocol should be prepared which defines the critical process parameters (CPP), critical quality attributes (CQA) and the associated acceptance criteria which should be based on development data or documented process knowledge. EU GMP Eudralex Annex 15- 5.21
Documentation: Validation Report
A validation report that cross-references the validation protocol should be prepared, summarizing the results obtained, commenting on any deviations observed, and drawing the appropriate conclusions, including recommending changes to correct deficiencies. EU GMP ICH Q7- 12.22
Conclusion: A Continuous Commitment to Quality:
Systems and processes should be periodically evaluated to verify that they are still operating in a valid manner. Where no significant changes have been made to the system or process, and a quality review confirms that the system or process is consistently producing material meeting its specifications, there is normally no need for revalidation. EU GMP ICH Q7- 12.6
References
1. ICH Topic Q 7 Good Manufacturing Practice for Active Pharmaceutical Ingredients
2. EudraLex, Volume 4, Part 1 Annex 15: Qualification and Validation
3. FDA, Guidance for Industry Process Validation: General Principles and Practices
4.WHO, TRS 986, Annex 2, WHO good manufacturing practices for pharmaceutical products: main principles
5. EU GMP EMA/CHMP/CVMP/QWP/BWP/70278, Guideline on process validation for finished products - information and data to be provided in regulatory submissions