Introduction:
Cleanrooms play a pivotal role in pharmaceutical facilities,
contributing to product safety, quality, and efficacy. These specialized
environments are meticulously designed and maintained to control airborne
particles, thus safeguarding the integrity of the products manufactured within.
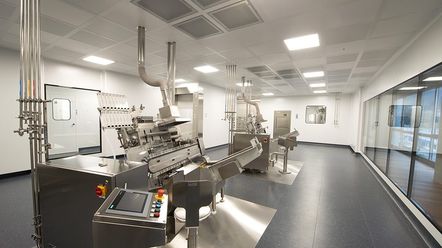
Defining Cleanrooms:
An area (or room or zone) with defined environmental control of particulate and microbial contamination, constructed and used in such a way as to reduce the introduction, generation and retention of contaminants within the area. (WHO TRS 961 Annex 5 Glossary)
Air Quality in Cleanrooms:
The air quality in cleanrooms is paramount to their functionality. Cleanrooms are equipped with filtered air supply systems that maintain positive pressure relative to the surrounding environment. This design prevents the ingress of contaminants into the cleanroom and effectively flushes the area. In addition, adjacent rooms of different cleanliness grades should maintain a minimum air pressure difference of 10 Pascals (EU GMP Annex 1 4.14). This stringent control prevents the transfer of contaminants between areas.
Gowning Requirements:
Gowning is a critical aspect of cleanroom operations. Gowning should be performed in designated change rooms with appropriate cleanliness grades to ensure that gown cleanliness is maintained. Outdoor clothing, excluding personal underwear, should not be brought into changing rooms leading directly to grade B and C areas, Facility suits and socks should not pose any risk of contamination to the gowning area or processes, A description of typical clothing required for each cleanliness grade is given in (EU GMP Annex 1 7.13)
Classification of Cleanrooms:
Cleanrooms are classified based on their level of cleanliness, with higher classes having stricter requirements for airborne particle control. The classification helps ensure that cleanrooms meet specific standards based on the products they produce. Reference for the classification and qualification of the cleanrooms and clean air equipment can be found in the ISO 14644 series of standards.
Adequate Systems and Filtration:
Adequate ventilation and air filtration are crucial components of cleanroom design. These systems are designed to minimize the risk of contamination and cross-contamination, considering air pressure, microorganisms (if relevant), dust, humidity, and temperature. Air filtration systems, including pre-filters and HEPA filters, are employed to maintain the desired air quality.
Air Change Rates:
Air change rates are set to ensure the defined clean area conditions are met. The appropriate air change rate varies depending on the cleanliness class and the area's purpose. Higher cleanliness classes, such as Class 10,000 and Class 100, often require significantly higher air change rates to maintain the desired air quality.
Pressure Differences:
Maintaining pressure differences is critical in cleanroom design. Adjacent rooms of different cleanliness grades should maintain a minimum pressure differential of 10 Pascals (EU GMP Annex 1 4.14). This positive pressure differential ensures that air flows from cleaner to less clean areas, reducing the risk of contamination.
Testing and Maintenance:
Regular testing and maintenance of cleanrooms are essential to ensure they continue to meet their required standards. Qualification processes for cleanrooms and clean air equipment include filter leakage tests, airflow tests, air pressure differential tests, airflow direction tests, and microbial contamination tests (WHO TRS 961 Annex 5 8.2.14). These tests help ensure that the cleanroom operates as designed and continues to meet the required standards.
Conclusion:
Cleanrooms are integral to the pharmaceutical industries, where product quality and safety are of utmost importance. Understanding the principles of cleanroom design, maintenance, and operation is vital to ensuring the production of safe and high-quality products. By adhering to these guidelines and standards, pharmaceutical facilities can maintain the highest levels of cleanliness and product integrity, ultimately benefitting both the industry and the consumers.
References
1. Volume 4 EU , Annex 1 Manufacture of Sterile Medicinal Products
2. WHO Technical Report Series, No. 961, 2011, Annex 5
Supplementary guidelines on good manufacturing
practices for heating, ventilation and airconditioning systems for non-sterile pharmaceutical
dosage forms
3. International Standard ISO 14644 Series